OMNI RANGE BURRS-METRIC
Overview of double cut burrs
Double-cut burrs, also known as cross-cut burrs, omni range burrs , are versatile cutting tools widely used in various industries for deburring, shaping, and material removal applications. With their unique design and characteristics, double-cut burrs offer several advantages and find extensive use in metalworking, welding, woodworking, and other related fields. Let's explore the features, applications, and benefits of double-cut burrs in more detail.
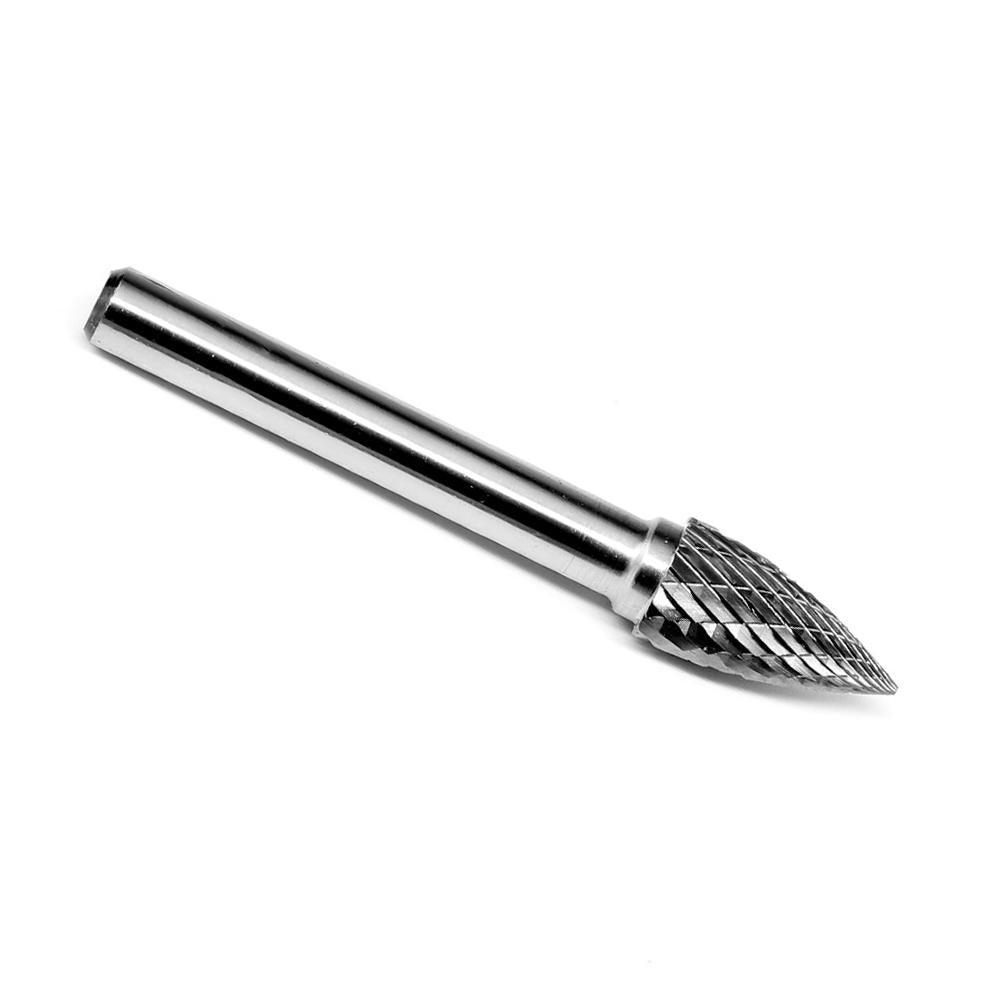
One of the distinguishing features of double-cut burrs is the presence of two sets of flutes that intersect each other, forming a crisscross or diamond-shaped pattern. This design creates multiple cutting edges, resulting in a more aggressive cutting action compared to single-cut burrs. The intersecting flutes enable faster and more efficient material removal, making double-cut burrs ideal for working with tougher materials and heavier stock removal.
Double-cut burrs are compatible with a wide range of materials, including ferrous metals like steel and iron, non-ferrous metals such as aluminum and copper, stainless steel, and harder alloys. They are highly effective in removing burrs, weld splatter, and excess material from machined parts. Whether it's deburring sharp edges, smoothing weld seams, or shaping metal components, double-cut burrs excel in providing precise and reliable results.
In metalworking industries, double-cut burrs are widely used for various tasks. They are commonly employed in metal fabrication, automotive, aerospace, and machining applications. Double-cut burrs are indispensable tools for tasks such as deburring, shaping, grinding, chamfering, and surface preparation. They help in achieving smooth, clean surfaces and precise contours on metal parts, both in production and repair work.
Welding applications also benefit from the versatility of double-cut burrs. These burrs are highly effective in removing weld splatter, smoothing weld seams, and preparing weld joints in metal fabrication and welding processes. Double-cut burrs ensure the production of high-quality welds and assist in achieving clean and well-prepared surfaces for subsequent operations.
While primarily designed for metalworking, double-cut burrs can also find applications in woodworking tasks. They can be used for shaping and carving wood, especially on harder or denser wood species. Double-cut burrs equipped with appropriate profiles and shapes allow woodworkers to achieve desired contours, intricate details, and smooth finishes on wooden surfaces.
Additionally, double-cut burrs prove useful in working with composite materials such as fiberglass, carbon fiber, and laminates. They assist in material removal and edge trimming during composite fabrication and repair processes, ensuring precise and clean cuts.
Double-cut burrs are available in various shapes and profiles to suit different applications. Common variations include cylindrical (straight), ball-shaped, tree-shaped, and cone-shaped double-cut burrs. The choice of shape depends on the specific task requirements and the desired outcome.
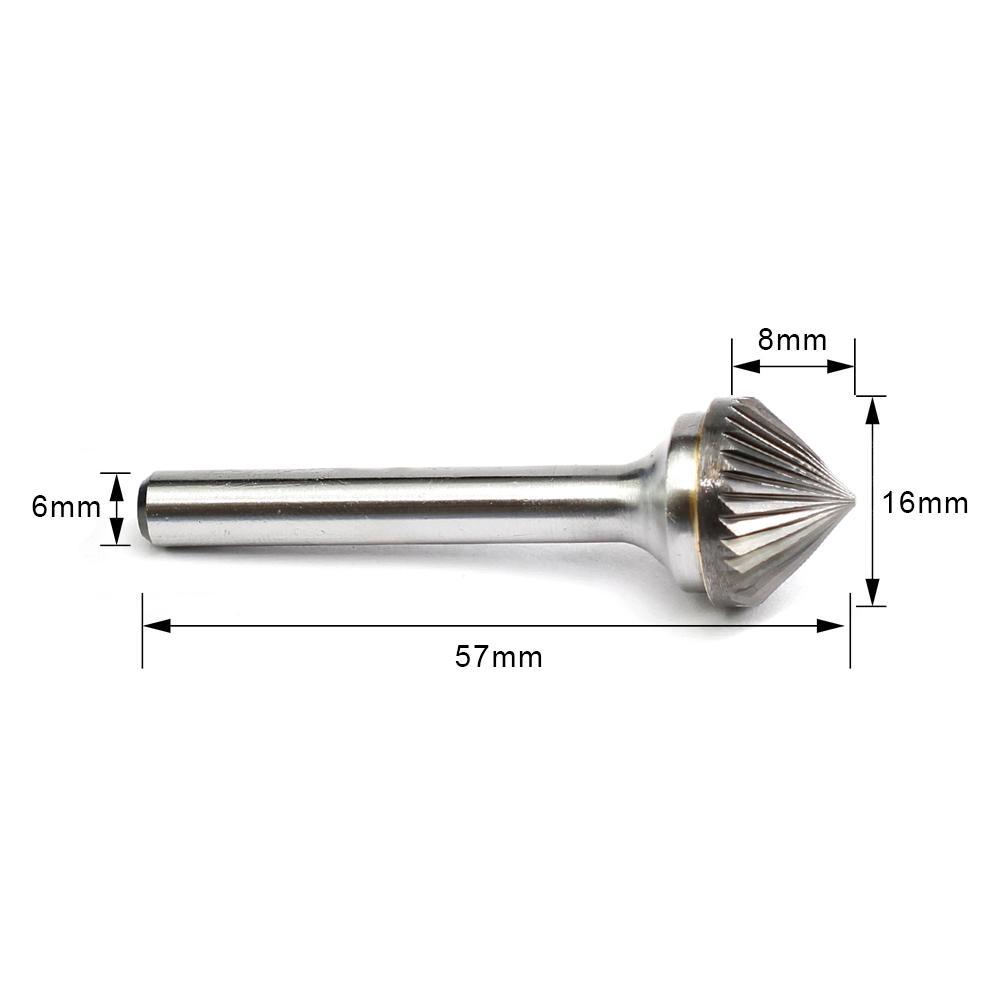
To ensure optimal performance and longevity of double-cut burrs, it is important to consider the operating parameters. Maintaining an appropriate speed and applying consistent, controlled pressure are key factors. Higher speeds and light, controlled pressure generally yield better results and help prolong the life of the burr.
In conclusion, double cut burrs are versatile, robust cutting tools that excel in heavy-duty material removal and deburring tasks. Their unique design, aggressive cutting action, and compatibility with a wide range of materials make them essential tools in various industries. By choosing the right double-cut burr and employing proper techniques, professionals can enhance productivity, achieve high-quality finishes, and improve overall efficiency in their respective applications.